Aftermarket Cruise Control for Classic Car - MG 1600
- JC
- Jun 26, 2020
- 4 min read
Updated: Aug 28, 2020
One of the more complex installs we recently had was a cruise control installation on a 1960’s MG 1600 MGA. The customer enjoys driving the vehicle regularly and on long trips so he decided to invest in a cruise control which would aid his comfort and would also make the car far more convenient to drive. The cruise control of choice was an Autostrada unit (Universal Fitment Part #4342) with an electric servo driven actuator. The kit comprised of the following:
Magnet kit (for speed pulse generator);
Clutch switch (to disengage the cruise control when the clutch is pressed);
Stalk switch (universal stalk for left or right hand mounting);
Electric Actuator with throttle cable;
Wiring Harness; and
Mounting hardware.

One other option for this vehicle was a vacuum servo however since this vehicle has twin SU carburettors it may not have had a very reliable vacuum source to power the vacuum operated servo. To ensure smooth and correct functions of the cruise control the best solution was to have an electric servo driven system.
The three biggest challenges we faced were:
Finding a suitable throttle cable connection to the twin SU’s (carburettors).
Speed signal generator location on the tail shaft that runs between the gearbox and the differential.
Fabricating a bracket for the clutch switch.

For the mounting of the stalk the customer wanted it on the left-hand side at an approximate 210 degree angle (or 8pm on the clock). Being behind the dash this position made it tricky to mount however easy to reach for the driver and it's out of the way so as not to obstruct anything in the driver's view or movement of his legs when pressing on any pedals or resting.

The stalk switch was mounted to the steering column using an “L” bracket and clamped with two large cable ties. The various buttons and functions of the stalk are:
Rotate the end of the stalk to turn the cruise on and off;
Rotate the end of the stalk to resume or coast;
The button on the end is the set (engage).
Connection to the brake circuit was wired into the factory brake switch which is pressure activated by high fluid pressure in the brake line. The speed signal is produced from the magnets on the tail shaft passing over the speed signal generator creating an inductive signal.

The supplied magnet from the speed signal kit was glued and cable tied to the tail shaft. When the tail shaft spins/rotates it passes over the pickup generating an inductive signal. One side of the inductive coil is ground and the other side is wired to the speed signal input of the cruise control.
The clutch switch is a mechanical stop bolt and its function is to interrupt the brake wire circuit connection from the cruise control.
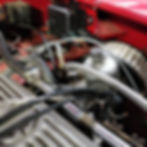
The actuator/ servo was mounted using nutserts (Rivet insert or rivet nutserts) making it easier to remove or re-fit as required. Off the front of the servo there is a throttle cable that connects directly to the carburettors. As this cruise control has an all in one unit PCB board, the main module is mounted inside the servo and there's a little port where you remove a rubber seal to access dip switches for settings of the cruise control
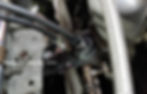
The biggest challenge we faced was connection of the new cruise control cable to where the original accelerator cable mounted. When the cruise control would engage and open the throttle on the vehicle there was a risk that it could dislodge the seating for the vehicle’s accelerator cable and could potentially jam the accelerator cable. To overcome this we had to make a bracket up and together with a clamp it would hold it in position so that it would not dislodge the factory accelerator cable. When installing the throttle cable try and leave some slack on the end of the cable allowing for adjustment of the accelerator cable. Allowing about 5mm of slack helps to slow down the initial throttle pull.

With everything now installed and the vehicle still on jack stands we then conducted some initial checks and testing. With everything functioning as it should we then took the vehicle on its first road test where we discovered that the initial configuration we selected of 1000 pulses was insufficient meaning the top speed was restricted. We therefore had to change the rate to 2000 pulses per mile. That has to do with the ratio of the differential. Normally differentials would halve the speed of the propulsion coming out of the tail shaft. So when you install magnets to a vehicle if you’re fitting them to a tail shaft you would use one magnet.

We also made adjustments to the sensitivity on the Autostrada cruise control which only has two settings available for high and low. We found that the high sensitivity was too high and after driving the vehicle the throttle pull was too aggressive. On low setting we found that the cruise control operated with a high degree of smoothness and steadiness of acceleration giving the car good drivability.
We discovered on our test drive that the cruise control was disengaging caused by suspension travel and subsequent tail shaft movement. So our next challenge was fine-tuning the clearance between the speed signal sensor and the magnet on the tail shaft to prevent the cruise from disengaging.
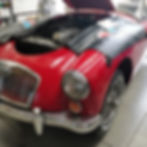
With the pulse rate and sensitivity now set the vehicle was tested extensively on high and low speed roads with varying road surfaces. We were pleased with how the vehicle drove and confident the customer would be happy with the results. In the months following installation the customer contacted us to inform us the cruise control was performing well and without any faults.